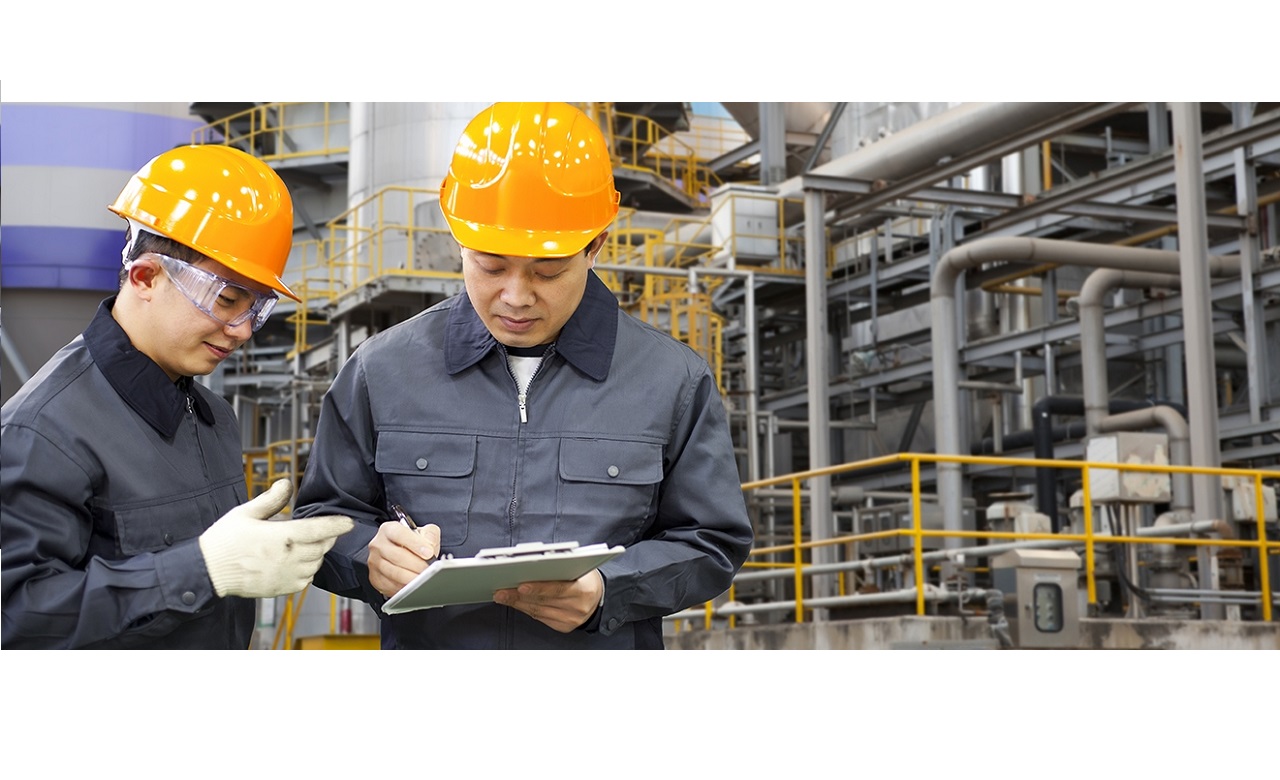
One of the most important things DeGATECH have learned over our years in helping people solve their industrial dust collection / Wet scrubbing problems is that many facilities have good equipment on site but the design and implementation of the equipment results in underperforming systems. Many of our clients want to know why their existing dust/wet collection systems have excess dust generation from pick-up points, experience frequent plugging in the ducts and allow dust buildup in process areas. This is where the DeGATECH system audits come in.
Our customers often ask us to visit their facility to review their current dust collection /Wet scrubbing system and provide a detailed audit and report that measures the current performance, identifies areas that can be improved and provides budgetary estimates for what those improvements will cost. There are many names for this process including: system audits, baseline assessments or gap analysis, but the basic goal is the same – to help our customers understand what they have now and how to improve performance going forward.
When contracted for this service DeGATECH will send their experienced engineer to your facility for an in-depth review of your existing dust collection /Wet scrubbing system or systems.
FEW OF THE MOST COMMON ISSUES WE IDENTIFY DURING OUR SYSTEM AUDITS
A TYPICAL SYSTEM CHECK VISIT INCLUDES
FOLLOWING THE SITE VISIT, DEGATECH PREPARE A COMPREHENSIVE DELIVERABLE PACKAGE THAT INCLUDE
This is one of our bestselling services ever and it is a great way to start gaining control over your dust collection systems. On average, our customers tell us they see an increase in their dust collector performance by 30% or more and longer times between shutdowns! Our engineers are trained to help you get more out of your current system by using the latest technological advancements, operating techniques and maintenance procedures